Cotton's water use
- Cotton’s average irrigation requirement is 6-7 megalitres per hectare.
- Australia’s cotton industry is one of the most water efficient industries in the world.
- Water-use productivity by Australian cotton growers improved by 52% since 1997.
Cotton’s average irrigation requirement is 6-7 megalitres per hectare (ML/ha) (source: Crop and Pasture Science 2013). This compares to the average water use of rice (11.5ML/ha), fruit and nut trees (5.1 ML/ha) and vegetables for human consumption (4 ML/ha) (source: ABARES).
Long-term monitoring shows the cotton industry’s significant improvements in water efficiency over time. Water-use productivity by Australian cotton growers improved by 52% since 1997.
The latest industry research shows these trends have continued and that Australian growers have continued to significantly increase yields and decreased irrigation inputs. NSW DPI, in partnership with the Cotton Research and Development Corporation, has been monitoring water productivity in irrigated cotton over the past three decades. This shows that:
- There has been a 97% increase since 1992 in the number of 227kg bales of cotton lint produced per megalitre of water, meaning growers are using just about half the water they used to, to produce each bale.
- The industry’s Whole Farm Irrigation Efficiency has significantly improved and is now 81% compared to 57% in the late 1990s, indicating more water than ever is being used by the crop instead of being lost on-farm.
Research into water use in the industry has continued and confirms continual improvement in water use efficiency, increasing yield while using less water.
The Australian cotton industry has achieved a steady increase in yield from less water over time, meaning more cotton fibre can be produced using less water per hectare than ever before.
Leading cotton producers can now grow nearly two 227kg bales of cotton per megalitre of water – almost double the industry average of a decade ago.
All water used on farm is captured through tail water recycling systems and is reused for subsequent scheduled irrigations.
Cotton Explained: Water allocations
Water use efficiency
The Commonwealth Scientific and Industrial Research Organisation (CSIRO) breeds cotton varieties appropriate for Australian and regional conditions. Each grower selects the best and most efficient variety for their region and farm.
Water-use productivity by Australian cotton growers improved by 52% since 1997.
The industry’s Whole Farm Irrigation Efficiency has significantly improved and is now 81% compared to 57% in the late 1990s, indicating more water than ever is being used by the crop instead of being lost on-farm.
Cotton is mostly grown in the 350-800mm rainfall zone, which means cotton crops can receive significant amounts of their water needs from rain during the growing season. In 2018-19, about 32% of the cotton crop area was rain-grown, the rest irrigated from ground and surface water sources.
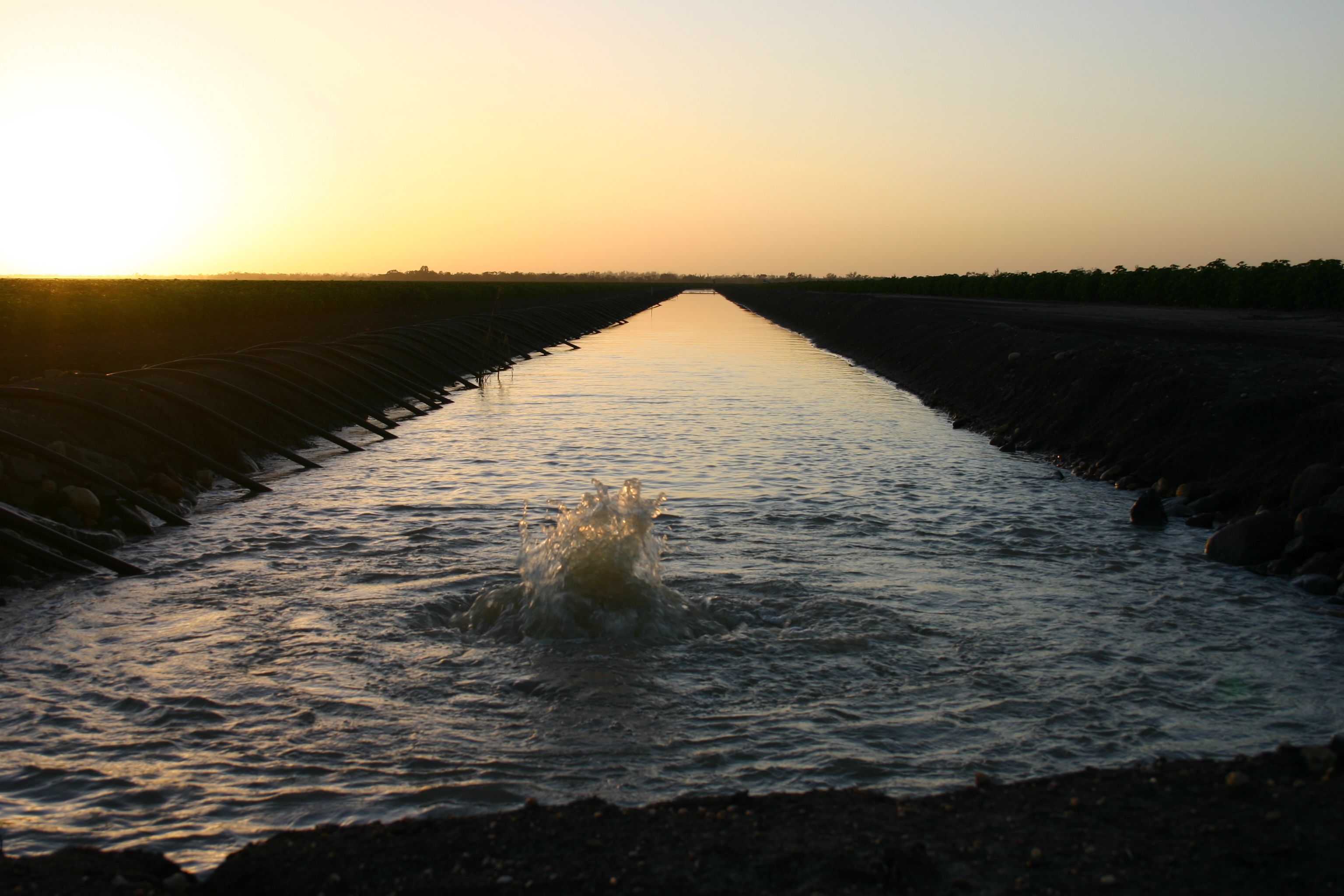
Research and extension
The industry has invested in research including:
- The Smarter Irrigation for Profit project, led by CRDC under the Australian Government’s Rural R&D for Profit program, involves a network of 19 farmer-managed learning sites around Australia. The first stage of this project found dairy, cotton, sugar and rice farmers could achieve a 10 to 20 per cent improvement in water productivity and efficiency by adopting new and existing precision irrigation technologies.
- Industry-wide water productivity is now being monitored and benchmarked annually. Regular measurement of this and other climate and crop management data allow deeper analysis into the effects of soil type, rainfall, temperatures, evapotranspiration, irrigation systems, establishment method, fertiliser rates, crop rotations and other factors in driving water productivity.
- The Keytah System Comparison, a grower-run project to assess the efficiencies of four different irrigation systems since 2009 to give growers detailed data to inform irrigation investment decisions. This has led to practice changes including:
- Efficient irrigation systems: in 2018, 25 per cent of growers were using overhead irrigation systems.
- Good field design: 83 per cent of growers maintained field slope in 2018, up from 61 per cent in 2014.
- Identifying field soil variation: 72 per cent of growers took soil characteristics into account in 2018 to help identify where water delivery improvements can be made, up from 41 per cent in 2014.
- Automation: in 2018, 27 per cent of growers reported using some form of automation, and a further 47 per cent said they are considering automation solutions.
(Source: Australian Cotton Sustainability Report 2019)
Cotton Australia statement - water theft
Cotton Australia condemns, without reservation, any unlawful action or activity associated with cotton growing in Australia including the misuse or theft of water resources.
Cotton Australia CEO Adam Kay has reiterated the peak body’s policy on water which endorses compliance with the relevant laws around water access and condemns illegal water take and illegal activity.
“Cotton Australia supports the role of the legal system in bringing to justice those found to have broken the law, and strongly backs the work of water authorities and regulators, in particular their enforcement activities.
“The vast majority of cotton farmers around Australia do the right thing and follow environmentally sustainable practices with water and other aspects of cotton farming including soil health and pesticide use. That’s why we have achieved significant improvements in water, pesticide use and yields over the past 30 years.”
Cotton Australia will take appropriate action against any grower found to have acted illegally in the production of cotton.